In this article
In manufacturing today, compliance is a full-time job. Across Australia and New Zealand, shifting standards, rising customer demands, and tighter regulations are turning compliance into one of the sector’s biggest pressures.
Whether it’s ISO 9001, HACCP, or medical device traceability, the margin for error is slim and the cost of failure is steep.
Compliance protects your license to operate, wins contracts, and safeguards your brand. Spreadsheets and paper trails no longer cut it; they expose your business to real risk. So, how do you stay ahead? Let’s break it down.
The compliance burden in manufacturing
Manufacturers today face a complex, evolving regulatory landscape. Depending on your sector, you may need to meet:
ISO 9001 (quality management)
HACCP (food safety)
FDA 21 CFR Part 11 for electronic records (essential in pharma or medical devices)
GMP (Good Manufacturing Practice)
Environmental sustainability standards (tightening across ANZ)
The list is long and constantly evolving. Updates to legislation, new customer requirements, industry certifications, and supplier audits all require manufacturers to stay alert and adaptable.
Non-compliance risks fines, stoppages, lost customers, even legal action. In some sectors, a single missed step, like a mislabelled batch or an out-of-date procedure, can trigger a costly recall or impact an entire supply contract.
Why traditional systems make it harder than it should be
Compliance failures aren’t caused by neglect but by inefficient, outdated systems.
If your quality team is still assembling compliance reports by cutting and pasting data across systems, chasing signatures manually, or filing crucial documents in shared folders, the entire process becomes fragile and time consuming and a serious risk.
Manual systems make it difficult to:
Keep accurate records across teams and lines
Track batch numbers from raw input to final dispatch
Retrieve documents instantly for audits
Stay aligned with new standards and policies
And when something does go wrong, like a failed audit or complaint, you are left scrambling through folders, inboxes, and paper trails trying to reconstruct the facts – wasting time and risking reputational damage.
Manual compliance processes simply do not scale. They are prone to error, hard to standardise, and stressful to manage, especially in fast-paced production environments.
Modern compliance needs a modern system
Compliance is hard enough. Your systems shouldn’t make it harder.
That’s why manufacturers are turning to Enterprise Resource Planning (ERP) platforms. An ERP brings together your production, inventory, quality, and compliance data into one secure, central system. For businesses in Australia and New Zealand, this means keeping pace with local standards and industry-specific regulations without the manual scramble. Compliance becomes part of daily workflows, not a last-minute scramble.
Manufacturers like Connec Operations have already seen the value of making the switch to a localised ERP. Facing strict compliance regulations for their configurable cable products, they needed a system that could reduce manual errors and manage every product variation with ease. As they put it:
We wanted a simple approach — we didn’t want to have an infinite number of paths for infinite configurations. MYOB Acumatica makes that process simple and accounts for all the slight variations in our bill of materials.
With MYOB Acumatica Manufacturing, businesses can:
Automate quality checks in production
Maintain real-time, audit-ready trails
Store documents centrally with version control
Trigger alerts when procedures fail
Track full product history from input to delivery
Instantly generate reports and certificates
Proof of testing? Done. Audit traceability? Ready in seconds.
And because it is cloud-native, your teams can access this functionality from the factory floor, the office, or wherever they are working. No lag, no confusion, and no more double handling.

It’s about more than avoiding risk
Compliance avoids penalties but its real value is strengthening the business.
When you are no longer tied up in admin and error checking, your team can focus on continuous improvement. You can move faster on new certifications, expand into new markets, or tender for work with stricter traceability requirements.
Compliance becomes a growth enabler, not a barrier.
Compliance confidence for Australian and New Zealand manufacturers
Regulatory complexity won’t disappear, but managing it can be simple.
MYOB Acumatica gives manufacturing businesses in Australia and New Zealand the visibility, traceability, and control needed to stay compliant and competitive. Whether you’re aiming to streamline audits, cut down on admin, or gain confidence that nothing’s slipping through the cracks, a connected cloud ERP is the smarter way forward.
And because we’re local, we understand the specific standards, pressures, and compliance frameworks you’re working with. We’re here to support you with tools that are built for ANZ manufacturing — today and into the future.
Discover how MYOB Acumatica simplifies compliance — so you can focus on building a stronger, more resilient business.
Contributors
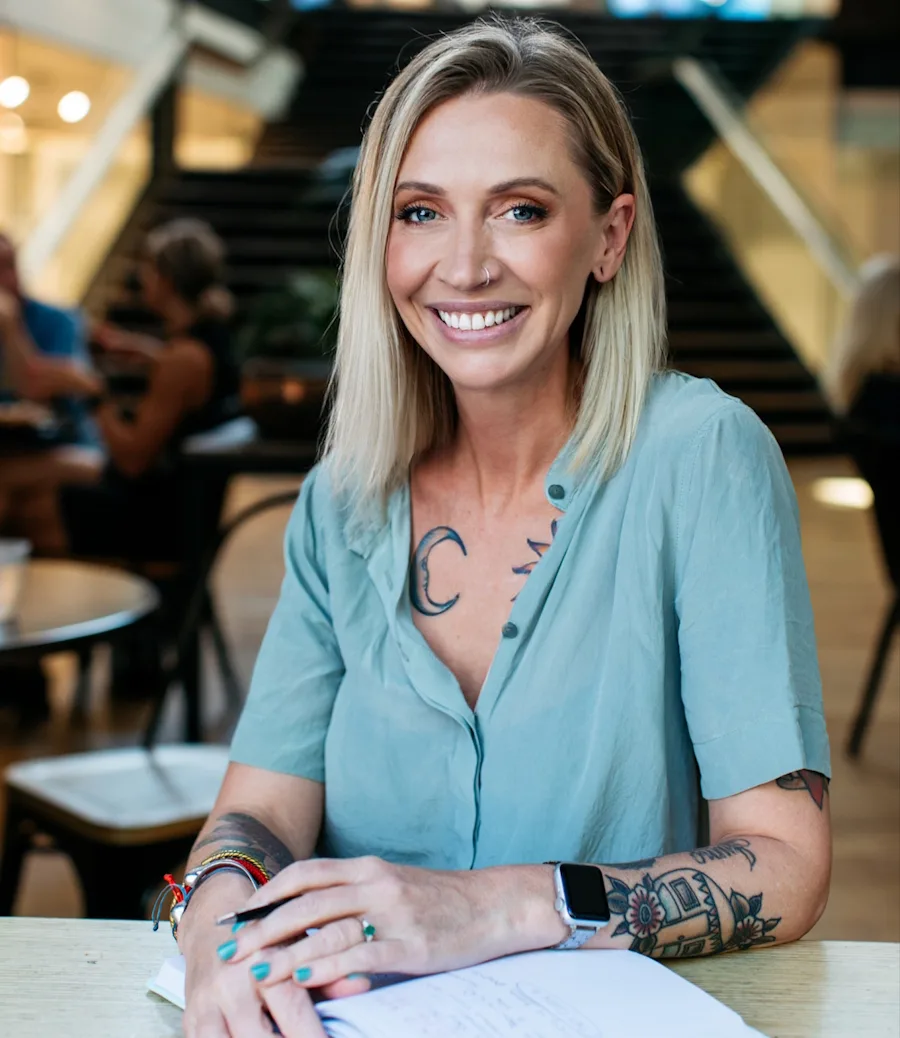
Senior Contributor