In this article
It’s 8:15 a.m. Your production manager is buried in spreadsheets, scrambling to reconcile stock movements, warehouse logs and supplier emails. A key delivery is missing. Production is delayed. Machines sit idle. Meanwhile, sales chase ETAs — and the day’s barely begun.
Idle machines, missed deadlines, and wasted labour are just some of the costs that quietly erode thousands from your bottom line every week.
For many manufacturers across Australia and New Zealand, this isn’t a worst-case scenario, it’s business as usual. Manual processes and disconnected systems create daily bottlenecks that drain productivity, squeeze margins, and hurt morale.
If you’re still relying on spreadsheets, whiteboards, and disconnected tools, these hidden costs are already adding up.
1. The bottleneck of disconnection
Disconnected systems don’t just slow you down; they create costly blind spots. When sales, production, inventory, and procurement work in silos, coordination becomes guesswork.
Need to confirm stock for a rush order? You’re chasing someone down. Scheduling production? You’re cross-referencing three systems and still confirming via email. When things change — as they always do — this approach fails.
Disconnected systems lead to:
Delays from manual data entry or conflicting records
Production errors from outdated material data
Procurement headaches from approvals and quantity rechecks
The problem isn’t your people. It’s the disconnected systems holding them back.
2. The cost of being in the dark
When systems don’t connect, decisions stall. Managers rely on outdated reports and guesswork — putting the business at risk.
Without real time insights, the impact adds up:
Production inefficiencies from overstaffing or idle machines
Missed deadlines due to overlooked supply issues or last-minute changes
Customer dissatisfaction from delays or poor communication
We unpack this further in our blog on why real-time visibility matters more than ever.
3. The hidden costs of manual workarounds
Manual tasks take minutes — but across teams, they add up to hours, dollars, and missed opportunities.
Let’s break it down:
Higher admin costs from double-handling and manual reporting
Downtime from miscommunication or overlooked scheduling
Inventory waste from over-ordering or obsolete stock
Poor resource use as skilled staff waste time on low-value tasks
4. From chaos to clarity: The case for ERP
The solution? A connected ERP platform.
An Enterprise Resource Planning (ERP) platform replaces fragmented tools with a single source of truth bringing your sales, production, inventory, and operations data together in one place.
That means:
Real-time updates on orders, capacity, and stock levels
One source of truth — no conflicting data
Automated workflows and approvals to cut delays
ERP becomes your business’s central nervous system — connecting every function for faster, smarter decisions.
MYOB Acumatica Manufacturing is a cloud ERP built for growing manufacturers. It delivers real-time visibility, eliminates double handling, and gives your team secure, anytime access — from the floor, office, or offsite.
Manufacturers like Kurrajong Kitchen are already seeing the difference. Owner Karen Lebsanft shares:
Before MYOB Acumatica, reports used to take us hours every month to compile manually. Now, it feels like they happen almost instantly. We can see the overarching picture — and trust that the number is right, instead of having to double-check it manually.

For Kurrajong Kitchen, moving to a connected ERP system meant faster reporting, greater confidence in their data, and more time to focus on growth and improvement — clear proof of how ERP can transform everyday operations.
And because MYOB Acumatica is cloud-native, your business gains built-in agility and every department is synced. Production changes trigger sales updates. Low inventory alerts procurement. No more spreadsheets. No surprises.
This creates a digital foundation that not only simplifies the present but scales with your business into the future.
5. Manual systems hold you back. Integration pushes you forward.
No manufacturer plans for disconnected systems. But what worked early on eventually holds you back.
Outgrowing your tech stack isn’t failure — it’s progress. A connected ERP cuts costs, drives performance, and frees your people to focus on quality and ultimately delivering better outcomes.
Bringing it all together
Manual systems aren’t just inconvenient — they’re a hidden liability draining margins and morale.
The right digital tools can unlock visibility, productivity, and growth. And if you’ve been struggling with spreadsheets and workarounds for too long, it’s time to ask yourself: what could your business achieve if everything just worked properly, all together?
Tired of running your factory on guesswork? Start your journey to a connected factory floor today.
Contributors
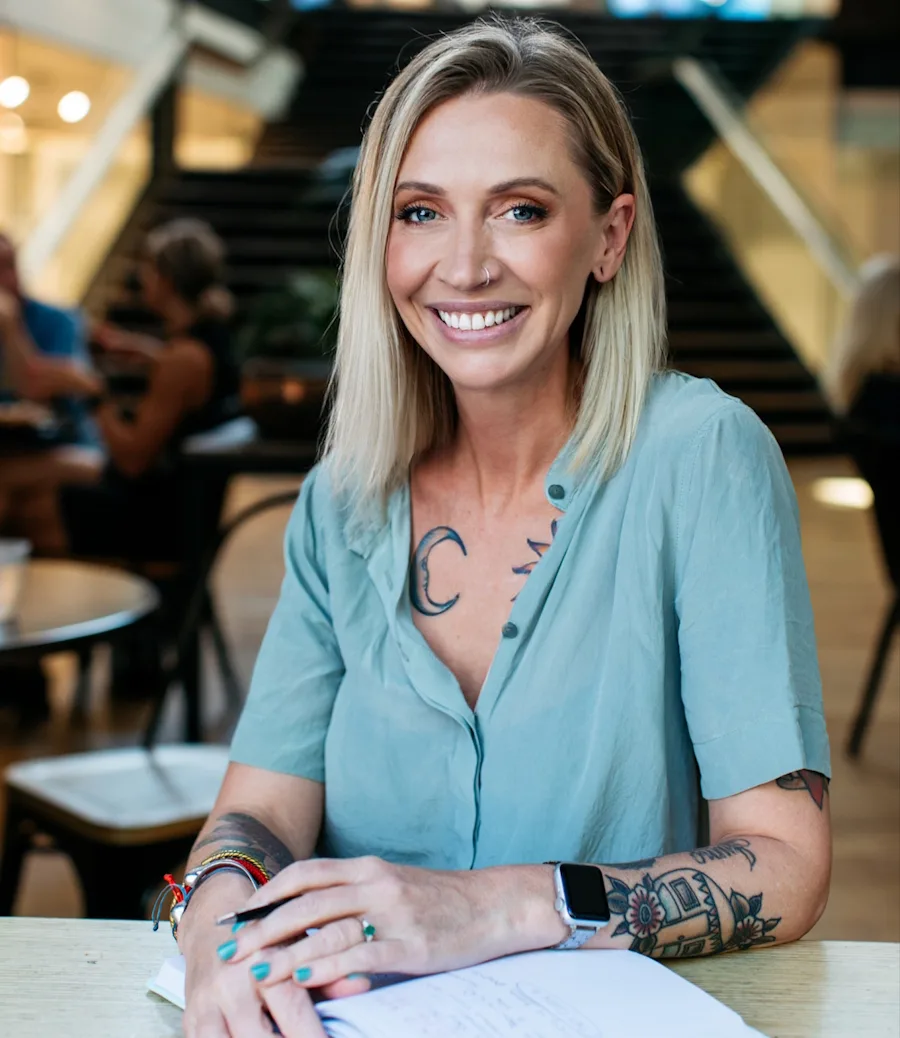
Senior Contributor