In this article
Balancing inventory is one of manufacturing’s toughest challenges: hold too little and risk production delays and lost orders; hold too much and tie up capital in idle stock, excess storage costs, and strained cash flow.
For manufacturing businesses across Australia and New Zealand, this tightrope walk between overstocking and stockouts is a daily challenge. And when manual processes or disconnected systems are involved, keeping your footing becomes even harder. Inventory management mistakes don’t just create operational friction, they can ripple across your entire supply chain, damaging margins, timelines, and customer satisfaction.
Let’s explore what’s really making inventory such a headache and how smart, connected systems can help manufacturers get back in balance.
Manual management: Why it’s holding you back
Many manufacturers still rely on spreadsheets, emails, and manual processes. While workable early on, these methods buckle as orders grow, product lines expand, and supply chains become more complex. The problem? Manual systems often lead to:
Inaccurate stock counts due to human error or missed updates
Slow response times when demand shifts or supply disruptions occur
Stockouts, which delay production, frustrate customers and cause reputational damage
Overstocking, which can tie up capital and increase storage costs
Inventory write offs from spoilage or obsolescence
Without accurate, real-time data, planners often rely on gut feeling or outdated spreadsheets to make purchasing and production decisions. And while spreadsheets might give you a snapshot, they don’t give you a system. As your production schedules become more complex, manual workarounds start introducing more risk than reliability.
Disconnected systems create blind spots
Even digital tools fall short if they don’t integrate. When systems don’t talk, you’re left with fragmented, unreliable data that blocks informed decision-making.
When systems are disconnected:
Teams rely on conflicting data
Stock levels lag, causing double orders or misaligned production
Procurement lacks usage insights
Sales overpromise, warehouses underdeliver
These siloes slow everything down and make it harder to respond to market shifts. If inventory is scattered across different systems, sites, or spreadsheets, it becomes nearly impossible to maintain the right levels, especially across multiple locations or product lines.
How ERP helps you master the inventory balancing act
A modern Enterprise Resource Planning (ERP) system transforms inventory control. It unites data across inventory, production, sales, and finance, giving every team real-time visibility.
A connected ERP system like MYOB Acumatica Manufacturing can support:
Smarter demand forecasting based on real trends
Automated, real-time inventory tracking
Live stock visibility across sites and production lines
Optimised replenishment suggestions
Scalability to grow with your operations
This means less guesswork, fewer stockouts, and better capital use. With ERP, the data does the heavy lifting, helping you make more confident, accurate decisions.
What smarter inventory management looks like
Imagine your purchasing manager gets a real-time low stock alert, reviews the system’s recommended reorder quantity, approves it, and keeps production flowing — no overordering, no delays.
Meanwhile, your sales team is quoting delivery times with confidence, because they’re working from live data. Your operations manager can see every item in every warehouse, its usage rate, and whether any slow-moving stock needs review.
This isn’t some far-off vision for the future. Manufacturers using ERP systems are already achieving this level of real-time visibility and control over their inventory. For Kurrajong Kitchen, moving away from spreadsheets and disconnected tools wasn’t just a step forward — it was transformative.
With inventory control, we can push a button and double-check anything. This gives us greater traceability on where things are. Now, we can see the overarching picture. You can trust that the number is right, instead of having to check it.

Their experience shows how the right systems can directly impact service delivery and operational performance — turning inventory management into a platform for scaling and building customer confidence.
Bringing it all together
Inventory might not always get the spotlight in manufacturing discussions, but its impact is undeniable. It sits at the heart of your operations — and when it’s out of balance, everything else follows.
To stay competitive, manufacturers need more than stock tracking – they need connected, intelligent systems that deliver visibility, reduce risk, and remove the guesswork from inventory management.
ERP systems like MYOB Acumatica are built to meet that challenge, supporting smarter forecasting, automated tracking, and agile planning. It’s not just about managing inventory better. It’s about building a manufacturing operation that’s leaner, faster, and more resilient.
Discover how a cloud ERP system like MYOB Acumatica can help you master your inventory and streamline manufacturing from the ground up.
For advice tailored to your specific needs, speak to one of our experts.
Information provided in this article is of a general nature and does not consider your personal situation. It does not constitute legal, financial, or other professional advice and should not be relied upon as a statement of law, policy or advice. You should consider whether this information is appropriate to your needs and, if necessary, seek independent advice. This information is only accurate at the time of publication. Although every effort has been made to verify the accuracy of the information contained on this webpage, MYOB disclaims, to the extent permitted by law, all liability for the information contained on this webpage or any loss or damage suffered by any person directly or indirectly through relying on this information.
Contributors
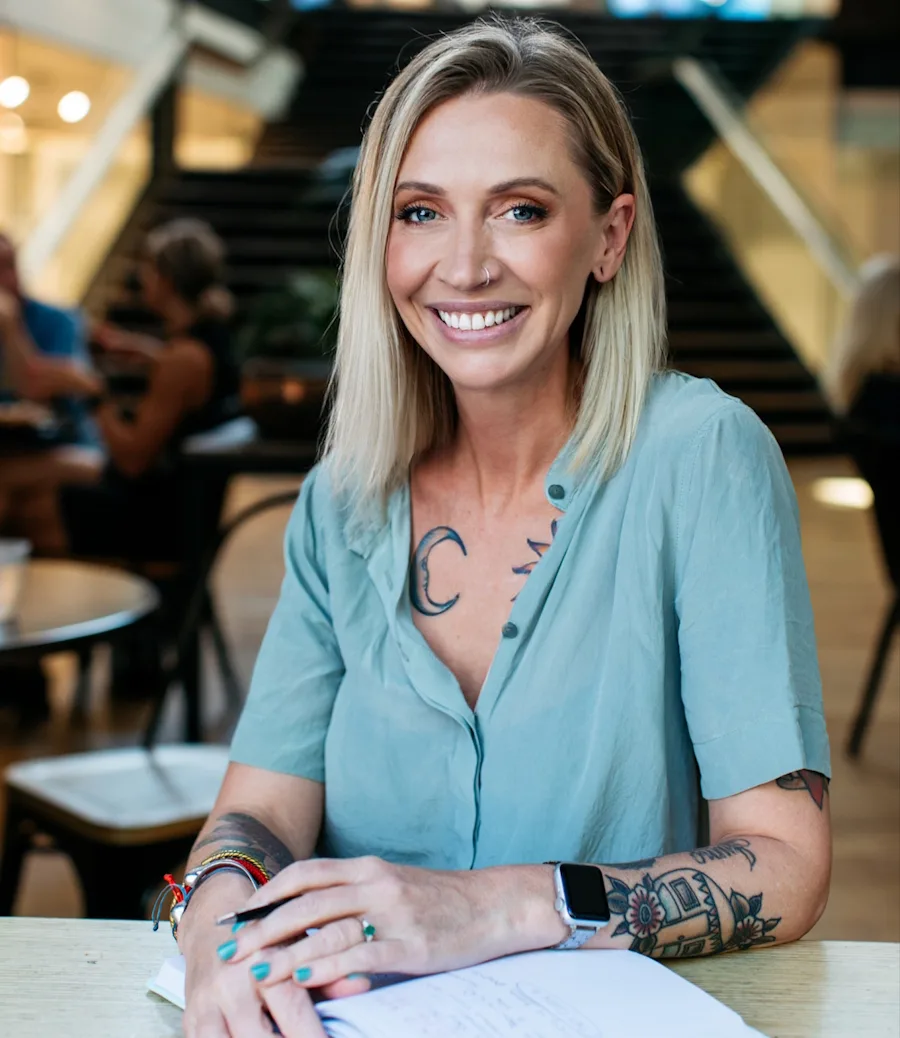
Senior Contributor